About 12 months or more ago I purchased an Aldi branded Work Zone variable speed 4" grinder which will take a 5" grinder disc . However its sat idle on the shelf and in the box since then.
The arbor which should hold the cutting or, grinding disc in place and centred was to small and the tab washer large even for the Adli Diamond cutting disc's I bought at the same time.
I could not find disc's to suit either. The arbor backing washer was stepped approx .5mm I didn't measure that at all.
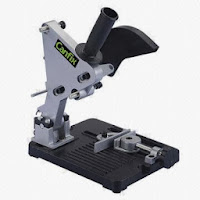 |
Grinder Cut Off Stand |
Although I still have my 30 year+ Hitachi 4" grinder there was a need to upgrade, my old one didn't have variable speed nor did it have the grip handle or the holes to mount one, I need to use two spanners to remove and replace the disc. I could not fit it to the Aldi Work Zone Grinder cut off stand.
I had been going to ask Ken if he could alter the arbor lock washer for me but when I bought the Myford ML7 I knew I could do it myself. or at least have a go So today being wet and miserable I set about doing just that.
I mic'd everything up the disc's I have, all measured approx 16.18mm or .637" except the Diamond Cut off discs they were 20.03 mm or .7885".
The Arbor washer measured 22.20 mm or .875" a difference of 6.02 mm or .238" thats a tad over 15/64".
Below is the Arbor and both sides of the arbor back washer, the rebate is to lock the washer in place on the arbor nut flats.
Metric and Imperial dimensions of the washer
Measuring the internal of the disc
Thanks goes to Neil (Hughie) who used the lathe on Friday and sharpened the HSS cutter to a point to suit his needs, I was able to get a very nice clean fine cut. When measuring 16.34mm the finished diameter and fitting the disc which sat snug.
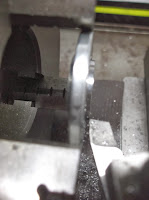
Set up on the lathe working this close to the jaws I don't mind saying I was uncomfortable with the clearance of the tool to chuck jaws. I checked averything at least six times turning the chuck by hand, moving the top slide and cross slide to make sure they would not hit each other.
Having seen pro fitters turners and engineers shave thou off washer this way I new it could be done either way
The safest way to have done this would have been turn up an arbor to mount the washer onto giving enough clearance.
The finished item below.
I now need to make either a spacer to take the Diamond cutter discs or a hole new arbor back washer........hum my skills are evolving which way to go? The back of the washer has a rebate to fit onto the arbor matching the spanner flats so it doesn't spin.
All done and put away after testing all is now good.
Photos of the reasons I like and bought the grinder.
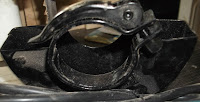 |
Quick release safety guard |
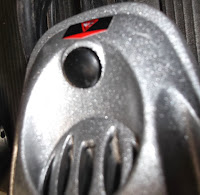 |
Push button spindle lock |
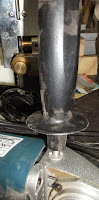 |
Additional handle and screw mounts allowing attachment to the grinder stand |
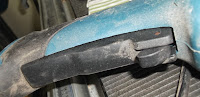 |
Safety lock on the forward of the switch the switch mounted at the finger tips. My old one has the switch mounted to the rear of the grinder a toggle switch and is a real pain to get too. |
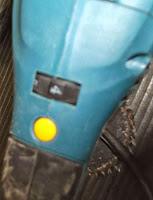 |
Variable speed control mounted on the top side |
I still yet have to use it cutting or grinding.