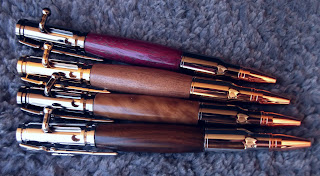
More recently she asked for a Bolt Action in Purple Heart.
Belinda had asked if I could do a matched Pencil. The Sierra does come in a twist kit yet none of my usual suppliers had them listed on their sites anymore. In chatting with Ian Dorney who runs Hunter Valley Custom Pens he had one to spare. Ian posted two kits down for me many thanks Ian I owe you one, well a few really.
The Purple Heart was supplied by Pat Keefe some time ago, Thanks Pat.
Belinda's birthday is just a fortnight away so I said again she can have this for her birthday.
Friday's is her day off I had her come over and we spent the morning making the pencil.
Belinda cut the blank, drilled it trimmed the ends and rough turned it and began to shape the Purple Heart blank, but with almost 1inch nails she found holding the Skew steady and her back was giving her a lot of pain she passed the remainder over to me.
Purple Heart (Peltogyne pubescens.)
Description
The heartwood of this South American timber starts of as a deep purple when freshly cut. It matures to a dark brown with time.Workability
Difficult to work because it is quite hard. Can burn on a wide belt sander if too much material is removed in one go.Applications
Traditionally Purple Heart had a wide range of uses including bridge building. In Australia it is relative expensive and is pretty much used for furniture. We did see some decking a few years ago but that was a one off.Availability
We keep limited stocks, all 25mm thick at present.Hardness
100Kg/m3 Particularly hard.Durability
Very Durable.At a Glance
Turning: | Excellent | |
Machining: | Difficult | |
Bending: | ||
Sanding: | Good | |
Nailing/Screwing: | Excellent | |
Glueing: | Good. | |
Timber Coating: | Accepts most finishes very well | |
Oil: | Fantastic with an oil finish. | |
Note 1 | A highly sought after cabinet timber. | |
Note 2 |
|